A couple of weeks back, I spent a weekend re-organizing my garage space, and part of that project included breaking out the welding cart so I could install an oxygen sensor bung on the exhaust (in anticipation of a future EFI system).
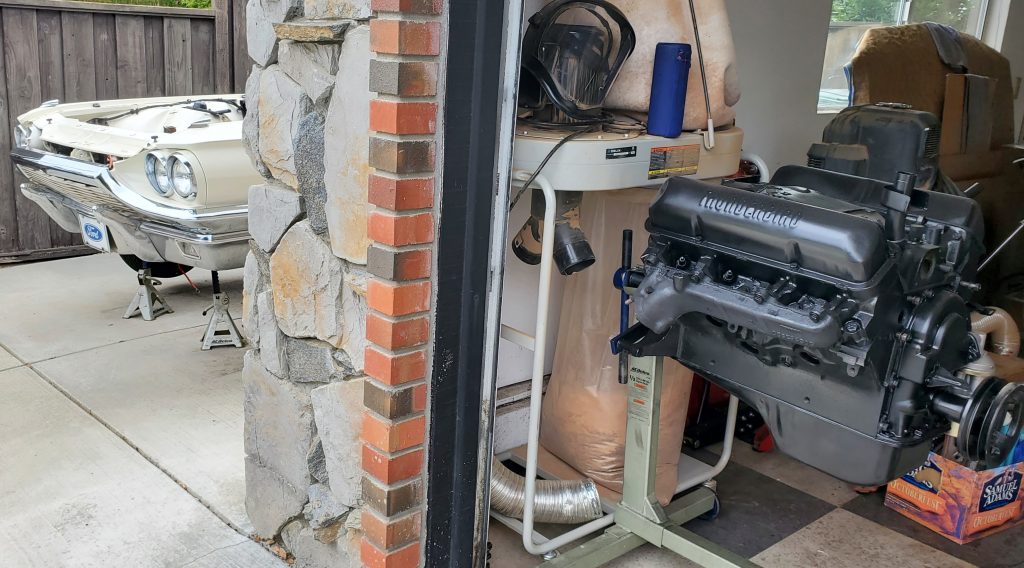
After a few practice welds (and remembering to turn on the gas for my MIG welder!), I felt comfortable enough to take a stab at the real thing. I made the opening with a step drill, then got a pretty good start welding the bung itself, at least from the side that’s easy to reach.
I had practiced getting the welding tip around between the fender and the exhaust, but when it came to the real thing, I realized that I had the setting sun at my back, and the glare inside my welding mask meant that I couldn’t see. I packed up my gear to wait for better conditions.
Later that night, I woke up and realized that I had left the exhaust flange on the wrong side of the bung!
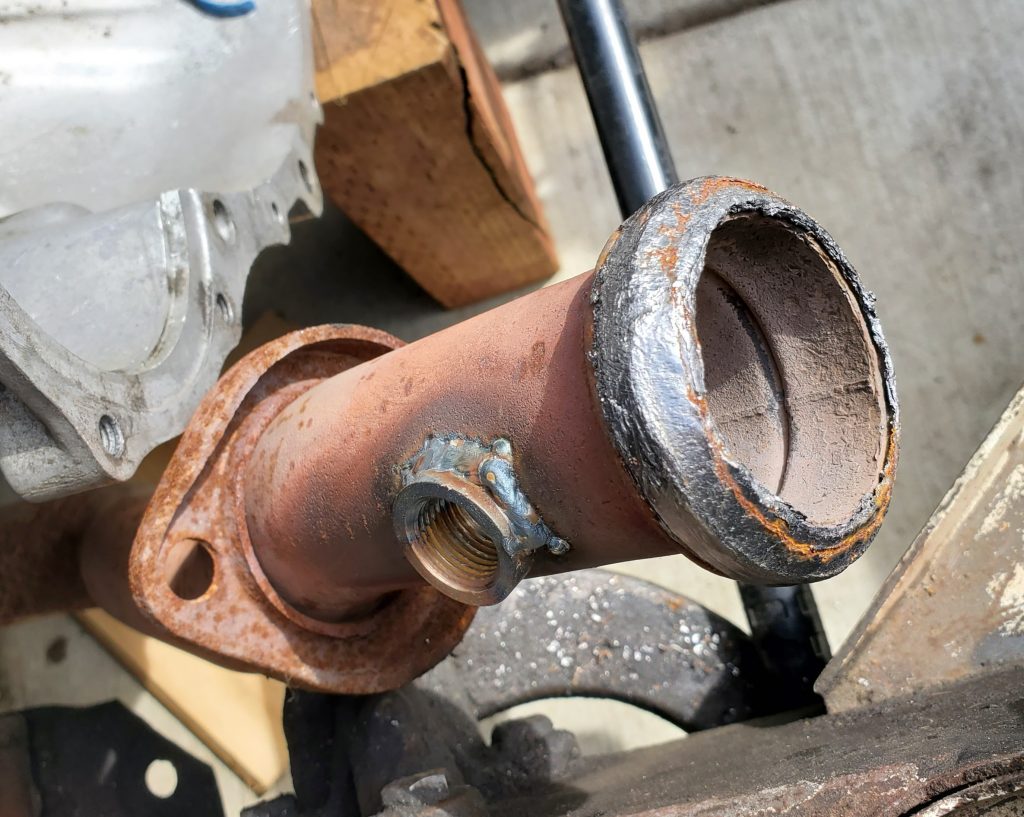
When the next cool overcast morning rolled around, I cut off the nicely welded bit, drilled the hole again and welded in another (after moving the flange). The new welds were not nearly as nice. I’m hopeful it’s sealed. If not, I’ll have to drop the exhaust to try again.
With the shelter-in-place orders not yet expired here, I decided to take a stab at installing the motor without an assistant. (My driveway has some slope to it, so my wife did stand by for safety’s sake most of the job.) I figured there’d be a lot of up-and-down—normally I work below while my son handles the hoist and topside work—and I was not disappointed.
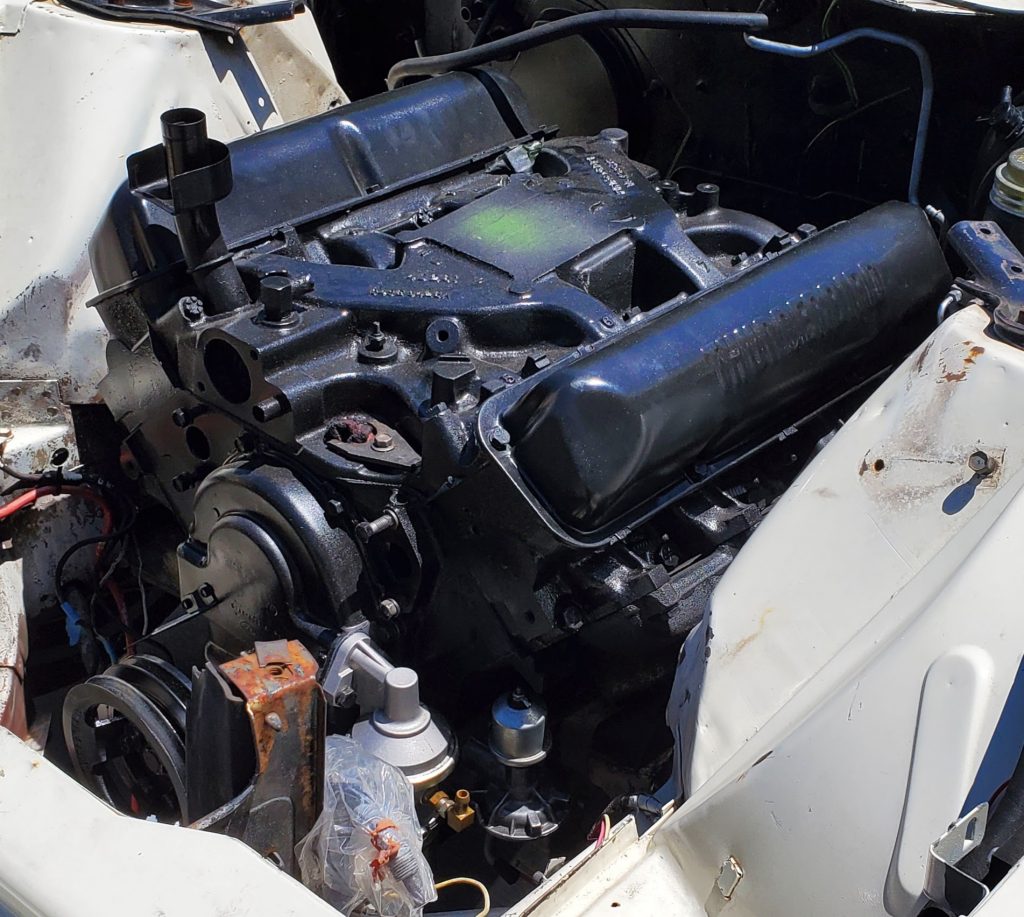
There was the usual frustration of working to get a bulky mass in just the right position, but also that satisfying moment when the engine comes together with the bell housing. Overall, installation took four hours including setting up tools beforehand. Much of that time was spent lining up and screwing in the engine mount bolts—a job that looks easy but is decidedly not.
There is much left to do before it’s ready to run: accessories to install, re-wiring part of the engine harness, hooking up the exhaust, and more. Looks like I have a shot at getting it running this month, though, which would be awesome.
I am following with interest. Are those Torque Thrust wheels? What size and offset did you go with? It appears there are few options when using the skirts.
Yes, these are Torque Thrust wheels: 15″ x 7″, -5mm offset, 83.06mm hub. I still run the stock drums all the way around. I modified the skirts a bit, but still get some minor rubbing in corners.
gday steve enjoying your posts i have installed fitech efi system on 64 tbird not as straight forward as advertised can send photos of set up and info on ironing out the gremlins we encountered if you like just email no probs mate
Regards adam gordon melbourne australia
Email sent!